На предприятии «Пензкомпрессормаш» начали выпуск нового оборудования
Генеральный директор одного из крупных промышленных предприятий Пензенской области Сергей Быченков дал интервью РИА «ПензаСМИ».
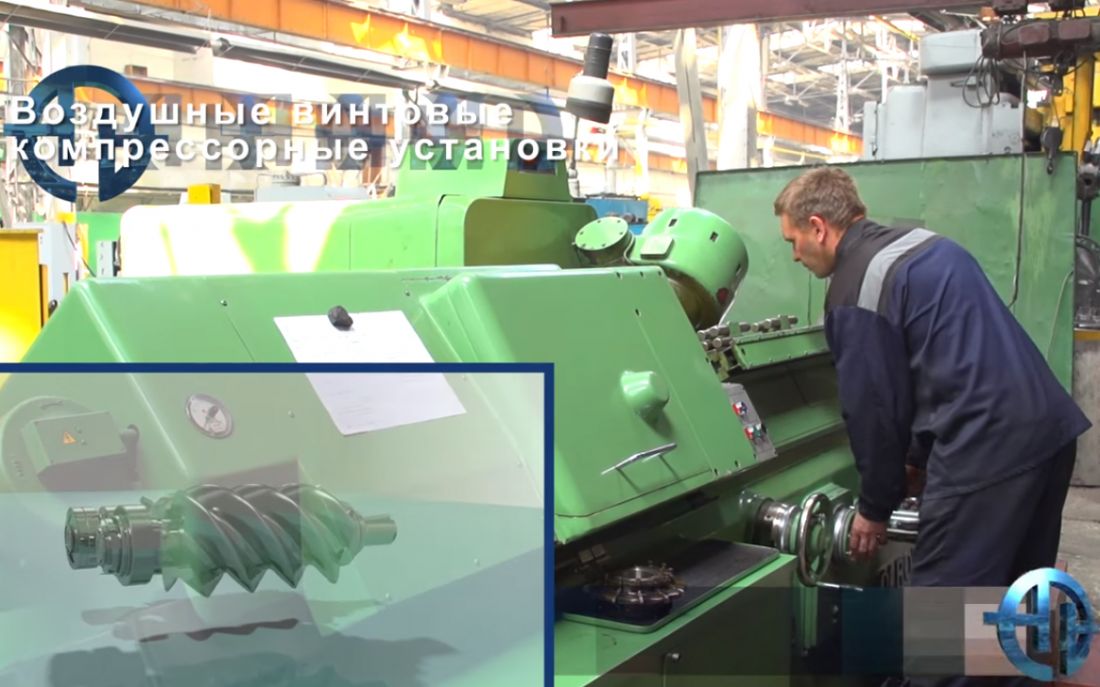
Фото: скрин https://www.youtube.com/watch?time_continue=57&v=JoCSQRktSNk.
- Сергей Геннадьевич, вы пришли на завод не в самое простое время. В 2015 году предприятие было убыточным, но уже вскоре после вашего назначения показало чистую прибыль порядка 60 миллионов рублей. Поделитесь секретом, как вам удалось этого добиться?
- Если так можно выразиться, в 2015 году убыток был не настоящий, а виртуальный. Дело в том, что завод выполнил заказ для компании из Узбекистана – выпустил три машины, но в самый последний момент заказчик отказался. Заказ на сумму 80 миллионов рублей остался на предприятии - это, во-первых. Во-вторых, возникли проблемы со сбытом тюбингов - элементов сборного крепления подземных сооружений для метро и тоннелей, на складе скопилось 900 тонн этой продукции. В сумме это принесло нам убытков на 120 миллионов рублей за год. Ну и объем производства был тогда совсем другим. В 2016 году у нас появился интересный совместный проект с «Пензхиммашем». Мы поставляли насосы – у нас есть собственное производство данного вида продукции - для Павлодарского нефтеперерабатывающего завода в Казахстане, где запускалась вторая очередь. Этот дорогостоящий заказ помог получить в 2016 году прибыль.
- Что Вы можете сказать про минувший год, каковы предварительные итоги по возглавляемому вами предприятию?
- Мы сработали на два-три процента лучше, чем в 2016 году. Один заказ с большими суммами планировали завершить до конца года, но по просьбе заказчика пришлось перенести сроки на март 2018. Если бы все сложилось, то в 2017 году сработали бы на 25-30 процентов лучше, чем в прошлом. Мы начали собирать серьезные компрессоры для перекачки газа и нефти. А вообще линейка у нас очень большая, насчитывает 80 наименований - от воздушных компрессоров до специальных. Последних делаем не очень много, но заказы есть. В 2017 году машины, которые в свое время не ушли в Узбекистан, мы продали в Северодвинск на крупнейший судостроительный комплекс «Севмаш». Это большие поршневые компрессоры, они уже прошли пуско-наладочные работы и получили одобрение заказчика. Запустили в производство новые воздушно-винтовые компрессоры марки ДВК собственной разработки. В ближайших планах сделать мегаваттный компрессор. Думаю, в этом году представим его для испытаний.
- Как Вы относитесь к кооперации с местными предприятиями? С кем удается сотрудничать, каковы результаты?
- Мы нашли взаимный интерес с компанией «СтанкоМашСтрой». Начинали с выпуска одного вида рам для их станков, потом произвели второй, третий. Вместе с генеральным директором Олегом Кочетковым съездили в Южную Корею, изучили аналоги и запустили собственное производство станин. В этом году планируем выпустить 700 тонн литейной продукции. Мы готовы к такому объему. Наш литейный цех после модернизации имеет производительность тысячу тонн в месяц. В целом для работы предприятия было закуплено пять станков. Один взяли у «СтанкоМашСтроя», в этом году готовимся приобрести еще два.
- Почему сроки изготовления компрессоров растягиваются на полгода и дольше?
- Быстрее не получится, это не от нас зависит. Некоторые проекты занимают год и больше: порядка шести месяцев уходит на подготовку документации, еще шесть — на изготовление самого компрессора. Есть воздушные компрессоры серийного производства, их делаем быстро. А есть специализированные, которые по требованию заказчика имеют обязательные комплектующие. Их приходится заказывать и долго ждать. Сегодня заказчики просят новшества. К примеру, крупный производитель полиэтилена низкого давления из Буденновска запросил современные внутреннюю систему отопления, пожаротушения, фонари на аккумуляторах – то есть свет погас, а они продолжают освещать. Мы раньше никогда такого не делали, но сегодня применяем эти интересные решения, нагружаем наше оборудование автоматикой. Сегодня появились российские производители, которые специализируются на изготовлении комплектующих. Что-то мы делаем сами – к примеру, базу, винтовые блоки. Отсюда доля отечественных комплектующих в нашей продукции составляет 80%, из них нашего собственного производства – 70%. Цель — выйти на объем производства в миллиард рублей за год, и мы это сделаем, нужно только время.
- С какими проблемами приходится сталкиваться российским машиностроителям, и какие, на ваш взгляд, требуют первоочередного решения?
- Ни один западный производитель не поставит в Россию оборудование с отсрочкой платежа – пока не заплатишь, никто продукцию не отгрузит. Но с отечественными производителями почему-то так не работают. «Газпром» говорит – вы нам поставьте оборудование, оно год у нас простоит, а потом мы решим, купить или нет. Компрессор стоит около ста миллионов. Для того, чтобы его изготовить и поставить, нужно вытащить средства из оборота. А что будет через год? Плюс НДС нам приходится платить сразу, как только отгружена продукция, хотя за нее еще полностью не расплатились. Мы гордимся тем, что большая часть налоговых отчислений в казну идет именно с промышленных предприятий. Но это тяжелая ноша. Зачастую предприятия не имеют оборотных средств, что приводит к банкротству. При этом с каждым годом налоги продолжают расти. К примеру, в Китае 17 процентов от доходов промышленные предприятия платят в виде налогов, но семь процентов им возвращают на развитие. Еще одна проблема — очень высокие платежи за электричество. В том же Китае плавка металла всегда происходит ночью, потому что электроэнергия в три раза дешевле. В 22 часа Шанхай погружается во тьму, гаснет вся уличная реклама, потому что начинают работать энергоемкие предприятия. У нас цена на электричество для производства неоправданно высокая.
- На ваш взгляд, что нужно сделать, чтобы отечественная промышленность развивалась в нужном направлении?
- Трудно сказать. К примеру, нам часто задают вопрос: «А что вы можете делать?». У нас возникает встречный вопрос: «А что вам нужно?». Раньше были проектные институты, которые связывались с заводами и планировали производство определенного оборудования. Сейчас есть свобода выбора, но она же ограничивает наши возможности. Я на должность гендиректора пришел с литейки, проработал там много лет. Считаю, что руководитель промышленной отрасли должен знать ее работу изнутри. Это видно на примере председателя правительства Пензенской области – Николая Петровича Симонова. Он промышленник, хозяйственник, изнутри знает, что нужно для развития промышленности региона. У нас есть оборонные заказы — порядка пяти процентов для военно-космических сил. Но мы на них ставку не делаем. Хотя за два компрессора, установленных на авианосце «Адмирал Кузнецов», мы получили благодарность. Наша задача – наладить выпуск востребованной конкурентоспособной продукции гражданского назначения и внедрять новые направления работы. Для развития необходимо привлекать молодежь. Без молодежи у завода нет будущего.